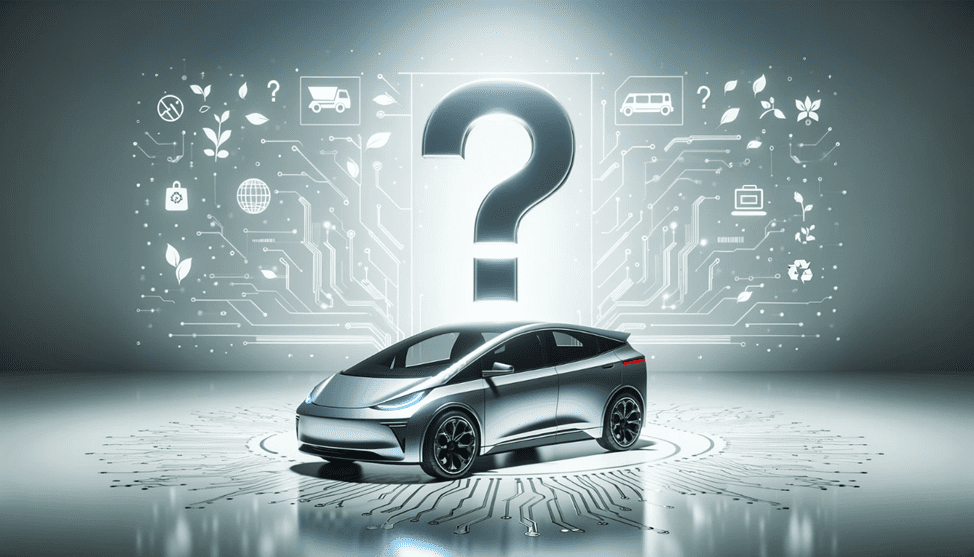
Introduction
Battery recycling has recently received significant funding from the public sector and automotive OEMs in the US and Europe. This funding aims to support the goal of increasing supply chain independence, in part by securing the supply of recycled raw materials. Despite the rapid adoption of battery recycling, the surrounding nuances of this process remain inadequately addressed.
In this article, we examine recycling as a method for battery disposal and debunk common misconceptions about battery recycling.

Pyrometallurgical recycling of batteries | Source: EE Power
Myth #1: Recycling Best Enhances Battery Sustainability
A commonly held view is that recycling is the most sustainable method for disposing of EV batteries. While certainly better than dumping batteries in landfills, it is important to realize that prevalent battery recycling technologies contribute substantially to greenhouse gas emissions.
The two leading battery recycling technologies are pyrometallurgy and hydrometallurgy, with some hybrid methods combining these two.
Pyrometallurgy involves heating steps like incineration, pyrolysis, and smelting, to recover nickel and cobalt from lithium-ion batteries. It offers marginal sustainability benefits over mining, consuming 80% of the energy and producing 90% of the greenhouse gases compared to mining virgin battery materials.
Hydrometallurgy, another recycling method, uses heated reagents to leach black mass and recover lithium, nickel, cobalt, manganese, and copper from pretreated batteries. Despite being cleaner than pyrometallurgy, it still results in 80% of the energy consumption and greenhouse gas emissions compared to mining.
Myth #2: Recycling Batteries is Highly Profitable
Another commonly held view is that recycling batteries is highly profitable. In reality, many widespread recycling technologies demonstrate low profitability today. In general, the economics of battery recycling vary widely and are dependent on the recovery rates of materials and the costs of the recovery process.
The recovery rates of materials from recycled EV batteries vary significantly across technologies. Hydrometallurgy can recover over 95% of lithium, nickel, cobalt, manganese, and copper, but only up to 10% of graphite. Pyrometallurgy recovers about 60% of nickel and cobalt, with minimal recovery for other materials. Processing pyrometallurgical slag with hydrometallurgy-like steps to recover copper and lithium adds significant cost.
The relatively high cost of material recovery limits profit margins. Hydrometallurgy in the US, Europe, and China sees profitability of ≤10%, often requiring subsidies. Pyrometallurgy, while having lower process costs, suffers from lower recovery rates, resulting in even thinner profit margins. The higher prices of recovered materials often drive up the procurement costs for feedstock, keeping margins very low even when material prices are quite high.
Myth #3: Recycling Feedstock is Abundant, and there is a Need for More Capacity
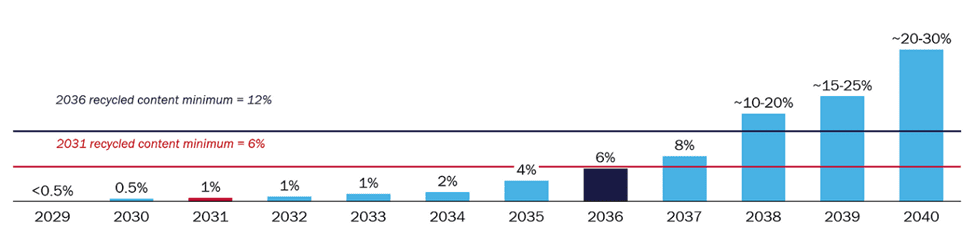
Required percentage of recycled lithium content in European EV batteries | Source: MIP analysis
The prevailing belief is that there’s a need to invest in battery recycling capacity to handle a surge of end-of-life EV batteries. This notion, however, relies on outdated assumptions about EV battery lifespans, often equating them with those of internal combustion engine (ICE) powertrains. In fact, we expect EV batteries to outlast ICE powertrains significantly, lasting 15-20 years before they cease to be functional for their initial use. Despite expectations of a considerable number of end-of-life EV batteries entering the market between 2025 and 2030, the capacity for battery recycling is increasing at a rate that currently surpasses the availability of these batteries. We predict that the existing or planned battery recycling capacities will align with the supply of battery feedstock only around 2033. In other words, it may take over a decade before the market has a sufficient quantity of depleted batteries to warrant the current expansion in recycling facilities.
Moreover, due to the extended lifespans of EV batteries, certain EU regulations, such as the recycled content mandates for new EV batteries (stipulating minimum recycled lithium contents of 6% by 2031 and 12% by 2036), could inadvertently disrupt the lithium-ion battery reuse and recycling market. The challenge lies in the potential unavailability of sufficient quantities of end-of-life feedstock within this timeframe, possibly incentivizing stakeholders to recycle batteries prematurely and leading to an artificial shortage of recycled battery minerals. As we will explore further, this premature recycling could undermine the economic value of batteries, as we believe they possess significant value before reaching the recycling stage.
Alternative: Second-Life Applications
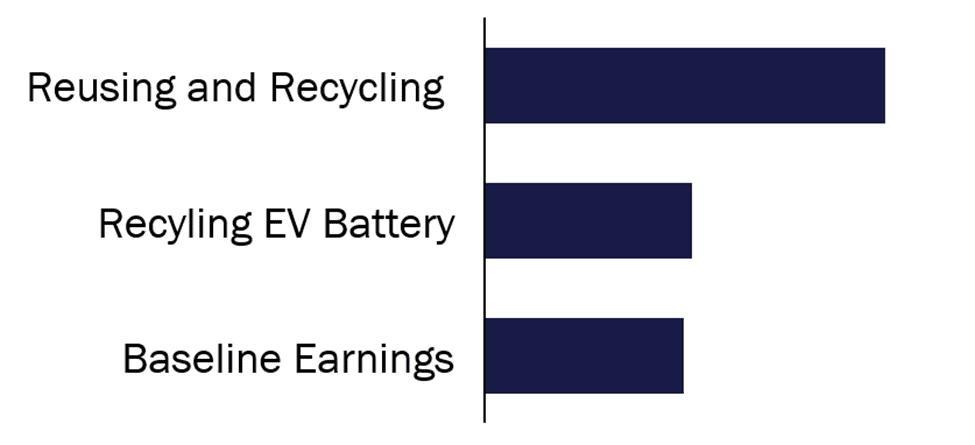
Lifetime earnings from reusing and recycling EV batteries versus baseline earnings | Source: MIP analysis
Second-life applications for EV batteries, such as energy storage systems, offer a more sustainable and economically viable intermediate step before recycling.
The carbon emissions from battery production are a sunk cost. Extending the battery’s life reduces the overall carbon intensity per unit of energy delivered by the battery. Approximately 70 kg of CO2 equivalent emissions are avoided per kWh of reused batteries.
Besides environmental benefits, reusing batteries in second-life applications offers substantial economic advantages. We estimate (and have seen) that reusing batteries before recycling can generate approximately twice the lifetime earnings compared to recycling alone.
However, successful implementation of second-life applications requires collecting and assessing batteries at the end of their first life, a role fulfilled by an emerging sector known as battery lifecycle managers.
We have previously delved into this topic in detail, which we encourage you to read.
Promising Future Technologies: Direct Recycling
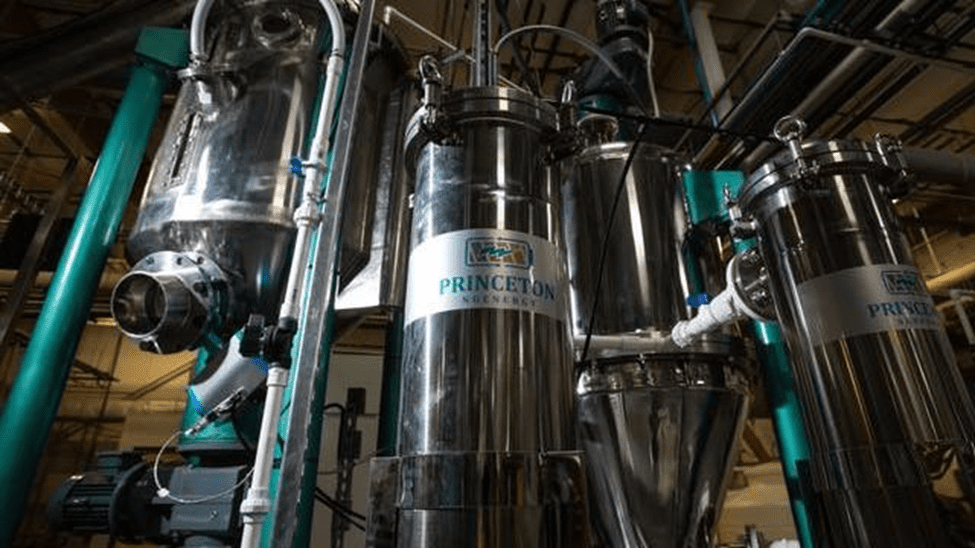
Direct recycling equipment | Source: Princeton NuEnergy
Direct recycling, an emerging technology, shows potential as a more environmentally friendly and profitable method of battery recycling.
Direct Recycling or Direct Cathode Recycling involves restoring the cathode material’s electrical performance without breaking it down into other compounds. The process typically involves two steps: obtaining a high-purity powder of cathode active material, followed by regenerating its electrochemical properties by reintroducing lithium.
Direct recycling could potentially reduce CO2 emissions, water usage, and energy consumption by up to 70% compared to mining battery materials. Besides its environmental advantages, direct recycling may offer higher profitability, with margins exceeding 15%.
Direct recycling significantly enhances the recovery rates of essential battery materials. This method can reclaim cathode active materials, such as lithium, nickel, cobalt, and manganese, with over 95% efficiency, while maintaining electrochemical performance on par with new (virgin) material. These recovery rates are either comparable to or exceed those achieved by hydrometallurgy. Notably, direct recycling achieves these high recovery rates at a considerably lower cost than hydrometallurgy, making it a more economically viable option.
Today, direct recycling is a nascent technology operating at a sub-scale. Its successful commercialization at a larger scale has yet to be demonstrated. However, we see potential in leveraging automation and advanced sorting technologies to boost the feasibility and scalability of direct recycling.
Recommendations for Stakeholders
We advise industry stakeholders, including OEMs, utilities, and energy storage providers, to collaborate with battery lifecycle managers. This collaboration aims to enhance the collection and reuse of batteries at the end of their first life. Furthermore, we urge policymakers to expand their understanding of battery circularity by integrating battery reuse as a core element of their strategies.
Additionally, we suggest that stakeholders investigate direct recycling technologies. These technologies offer a way to increase recovery rates, enhance profitability, and decrease emissions. At MIP, we have pinpointed several key technologies that could facilitate the growth and scalability of these emerging methods.
Lastly, we recommend a thorough reevaluation of the timelines set for recycling content mandates. Decisions regarding investments in further pyrometallurgy or hydrometallurgy capacities should be made after carefully considering the timing and the value chain dynamics of feedstock availability, as well as the relative benefits versus emerging recycling technologies.
About MIP
MIP is a collaborative strategic investment firm that brings together the leading stakeholders in the mobility ecosystem — auto companies, parts suppliers, energy companies, fleet operators, logistics providers, technology and communications companies, financial and insurance companies, as well as cities and municipalities — to identify common challenges, find solutions, invest in those solutions, and then scale those innovations across the market.